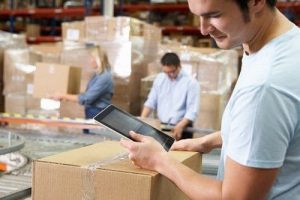
A Focus on Ergonomics Prevents Injuries in Your Warehouse
Workplace injuries put employees’ well-being at risk and can cost your business a considerable amount of money. Adopting ergonomic practices and investing in tugger carts and other equipment can help reduce these risks. Keep the following in mind in order to improve workplace safety at your warehouse.
Placing Items
Warehouse workers are at risk of injuring their back or other parts of their body while picking up items and moving them to another location. You can reduce this risk by having employees use lifting mechanisms to retrieve items that are heavy or large. Using carts for picking items that are on or near ground level also helps lower the risk of injuries.
Packing Items
Items that are bigger or heavier can put workers at risk of being injured while they are packing them. Workers can also be hurt after items are packed if they are not in a secure crate or container. Ensuring that workers have equipment for packing large or heavy items and putting them in secure crates or containers helps keep employees safe from injuries on the job.
Shipping and Receiving Items
Workers can become injured while removing large or heavy items from pallets. Ergonomic practices that reduce this risk include having mechanical equipment available to handle the task of lifting and moving heavier items. Making sure that items being shipped are placed in secure containers and crates can also help lower the risk of warehouse employee injuries.
If you are interested in tugger carts for your warehouse, please contact DJ Products. Our carts can make it easier and safer for employees to move heavy equipment and items.