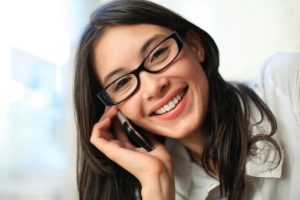
For the first time in 46 years, the U.S. Department of Labor has updated the regulations regarding sexual discrimination for defense contractors and all other federal contractors. Covering issues like pregnancy of employees and transgender status, the new rules apply to any federal contractor that receives a minimum of $10,000 from government contracts in a one-year time frame. Also covered are unlawful employment practices that treat women differently than men in the workplace.
Today’s workplace and legal landscape
It’s imperative that corporations embrace diversity in the workplace to protect all employees from any form of discrimination and a hostile work environment. To minimize the possibility of injuries to personnel and to help them complete their work efficiently, DJ Products, Inc. provides a full line of DOD contracting equipment. Designed specifically for the unique demands of defense contractors, this powerful equipment is easy to maneuver and it operates quietly. The BombCaddy offers dual-mode, remote-controlled power to intricately maneuver up to 5,000 lbs around tight areas and heavy equipment.
Federal contractors have no reason to feel uncomfortable about the newly adopted rules. Most DOD contractors and other company owners are already making decisive efforts to eradicate outdated stereotypes. These updated regulations help address any lingering issues of pay discrimination or uncertainty about dealing with gender identity and transgender status.
At DJ Products, our goal is to provide electric and motorized solutions that will eliminate strains from attempting to push or pull heavy loads. To learn more about our walk-behind and remote controlled DOD contracting equipment, contact us today to speak with one of our equipment specialists about solutions tailored to your business.