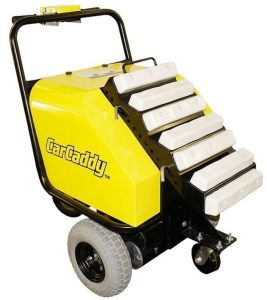
When you own a car dealership, it may seem as though you shouldn’t have any real concerns about safety. When your employees aren’t in the office, they’re probably working with customers on the floor, taking them on test drives, discussing service, etc.
Even so, here at DJ Products we believe there are safety concerns in every business, and the dealership is no exception. In some ways, because the risk of safety problems seems so low, we remind all business owners to remain diligent. An insurance company by the name of The Zenith recently came out with several forms that are available online for you to use in your dealership’s safety program.
Moving Cars Safely
At some point, your employees will have to move cars for one reason or another, and it may not always be feasible or even possible for them to get behind the wheel. In these instances, a dealer caddy (car pusher) is a perfect solution that was developed for car dealerships. It’s a great resource because it saves employees’ backs and keeps you from having to compensate them for potential injuries.
Moving Parts Safely
Don’t forget your employees in the warehouse and the service department. They often take delivery of large bulky items when your parts are received, and carrying those heavy pieces back and forth to the shelves can take a real toll on their bodies. Instead, a parts caddy can help them stay safe and do their jobs much more efficiently.
Whether you’re in need of a car pusher for car dealerships, or just about any related business, contact us at DJ Products to help.