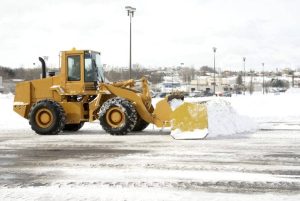
It’s not just warehouse equipment that suffers the ill effects of cold weather. When the temperature drops, employees are vulnerable to a number of physical conditions ranging from non-threatening to serious.
How do you protect your workforce from the effects of winter? Follow these guidelines to keep employees safe during cold weather conditions.
Understand Cold Stress
Cold stress occurs when frigid temperatures and wind combine to lower skin temperature, eventually leading to reduced internal body temperature. Dampness can accelerate the process.
Monitor the Weather
Appearances can be deceiving. It’s not enough to go by the air temperature. Wind chill allows for the factor of wind speed, which can make actual conditions even colder than what the thermometer shows.
Train Employees
Supervisors should:
– Keep a close watch on employees for signs of cold stress
– Assign workers in pairs or groups
– Allow frequent breaks in warm, dry areas
Employees should:
– Learn to recognize conditions that promote cold stress
– Learn what to do if they or co-workers begin showing signs of exposure
– Dress in appropriate clothing and accessories
Know the Signs
– Trench foot results from exposure to wet and cold for long periods of time. Symptoms include red skin, numbness, tingling and cramps.
– Frostbite begins as reddened skin and progresses to patches of gray and white.
– Hypothermia is characterized by uncontrollable shivering, while more serious cases can cause slurred speech, clumsiness and confusion.
DJ Products: Your Year-Round Source for Warehouse Equipment Moving Solutions
In any type of weather, musculoskeletal stress is the number one cause of workplace injuries. We offer a comprehensive line of electric warehouse equipment movers designed to reduce the risk of lifting and repetitive motion tasks.
Call 800.686.2651 to learn more from our helpful sales engineers.