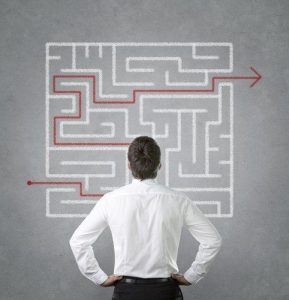
Warehouse managers are responsible for a wide range of tasks in order to keep their operation running as smoothly and efficiently as possible. While some leaders don’t mind overseeing employees and finding ways to encourage them, others would rather spend their time handling tasks, such as selecting new equipment for warehouses.
If you’re among those who don’t necessarily enjoy being in charge of others, you can still be an outstanding manager. The following tips can provide you with some insight on how to make the most of your skills.
Focus on Problem Solving
One of the most effective ways to ensure that your warehouse keeps running as efficiently as possible is by putting an emphasis on problem solving. Have workers engage in coming up with ways to handle problems that come up in day-to-day operations. Having challenges to face at work can provide workers with motivation to do their best on the job.
Delegate Leadership Tasks
When possible, find employees that have earned your trust by proving to be dependable and highly competent. Assign certain leadership tasks to these employees rather than having to handle all of them on your own. Giving these tasks to trusted employees helps boost morale in the workplace while also giving them a reason to trust and respect you.
Improve Communication
Having solid communication skills is one area that you can’t compromise on. If you struggle with communication, work on improving those skills in order to encourage your workers to put forth their best efforts on the job.
If you need high-quality equipment for warehouses that helps improve safety and productivity, contact DJ Products. We carry a wide selection of equipment that allows your workers to do their jobs more efficiently.