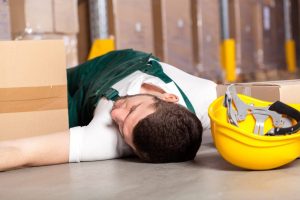
As a leading supplier of material handling equipment, one of our main goals at DJ Products is helping to improve workplace safety. If an employee becomes injured on the job, your response can be a critical factor in limiting the severity of the incident.
Use this checklist to make sure you’re following the appropriate steps to handle a workplace injury.
1. Obtain Medical Attention
At this point, the employee’s health and physical attention should be your overriding concern. Prompt medical attention can mitigate injuries and reassures workers of your interest in their well-being.
Call 911 if you even suspect the injury is serious. It’s best to err on the side of caution. If the injury is obviously minor, you should still encourage the employee to seek medical care.
2. Document the Incident
You’ll need to provide detailed reports for Workers’ Compensation as well as any information required by your company’s specific policies. Don’t forget to take pictures and interview any employees who were involved as witnesses.
Injured employees have the right to file a claim, so provide them with the form promptly and report it to your workers’ compensation insurance company. Never give information to anyone but your insurance carrier and their attorneys.
3. Welcome the Employee Back to Work
Terminating or penalizing an employee for an workers’ compensation claim can open your company up to major repercussions.
4. Take Steps to Prevent Future Incidents
How could the accident have been avoided? Evaluate the situation and make any necessary changes.
DJ Products: Your First-Choice Supplier of Material Handling Equipment
Our battery-powered tugs and movers minimize risk of injury from pushing and pulling, the number one cause of workplace injuries. Visit our website for more information.