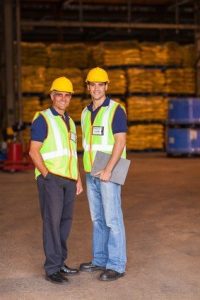
When it comes to warehouses, lean and mean is the order of the day. Faced with flat or negative growth, supply chain executives are turning to updated material handling equipment and other strategies to reduce labor costs while maintaining high levels of customer service.
Here is the conclusion of our two-part look at effective tips to improve order picking efficiency.
How to Maximize Order Picking Productivity
Set Up “Hot Zones”
In an earlier tip, we talked about the importance of reducing the amount of time it takes order pickers to travel through the warehouse. One way to do that is to set up “hot zones” where higher-velocity items are concentrated.
Some companies find it useful to implement an ABC analysis that assigns items to one of three categories based on velocity. Another option is to widen the aisles where the higher-velocity items are located to prevent congestion from multiple order pickers.
Use Appropriate Storage Media
Warehouse efficiency can be measured by the number of times an item is handled from the time it arrives until the time it leaves. That rate goes up when product is stored in the wrong media, such as when slow-moving SKUs are slotted in pallet racks.
Cube movement velocity is calculated by movement in units times cubic dimensions. Use this metric to determine the optimum storage medium for each SKU.
Quality Material Handling Equipment for All Applications
Our battery-powered material handling equipment lets a single worker safely and quickly move loads weighing thousands of pounds. We have a full line of tugs, pushers and movers, including models that can accommodate awkward loads such as drums and carpet rolls.
Visit our website to learn more from a helpful member of our sales engineer team.