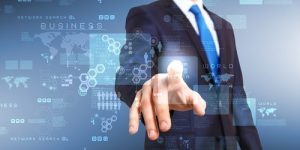
Are robots on your list of must-have warehouse equipment? They might be soon, thanks to an innovative California robotics start-up that’s targeting the warehouse logistics industry.
Fetch: The Evolution of a Robotics Company
Fetch, located in a modest office park in San Jose, rose from the ashes of Willow Garage, a robotics hardware company known for its PR2 platform. The PR2 was a Jetsons-like robot designed for both home and business use.
When Willow Garage folded in 2014, some of its staff members joined forces to found Fetch that same year. Fetch built capital from sales of its Mobile Manipulator and Freight Mobile Robots, which were patterned after the PR2 and sold largely to universities.
According to CEO Melonee Wise, the company decided to move beyond the scope of Willow Garage and focus on manufacturing and warehouse applications. Wise explains that they studied the market and discovered that the industry “looked like a pretty tractable problem” that could benefit from a robotics solution.
The Future of Robotics in Warehouses and Logistics
The team at Fetch is addressing this need with a round, modular hardware platform on wheels that’s been compared to an “oversized Roomba.” On-board intelligence systems guide the robots through a “semi-structured environment” while avoiding co-workers, both human and mechanical.
Other features include a proprietary cloud control platform and a graphical interface that make operations easy for non-roboticists. Wise says future plans include development of a system that can actually pick up and place objects, a skill long considered the “Holy Grail of robotics.”
State-of-the-Art Warehouse Equipment from DJ Products
Maximize manpower with our battery-powered tugs, movers and pushers that allow a single employee to move loads weighing thousands of pounds. Contact us for more information.