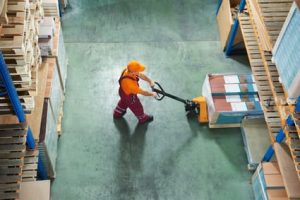
You stock your facility with the warehouse equipment necessary to keep employees safe. Unfortunately, even small issues can result in serious injuries to workers when overlooked. Though accidents will happen, making staff aware of safety hazards and arming them with the proper training and tools minimize risks.
Four Commonly Overlooked Warehouse Hazards
The most common warehouse hazards are:
1. Pallet Rack Collapses: Pallet rack collapses occur when materials aren’t stowed in an orderly manner. They are exceptionally dangerous when resulting from high tiers, where even small items can become dangerous projectiles with momentum. Stacking items/pallets with the heaviest/largest items on the bottom and lightest/smallest on top, firmly positioned and wrapped with adequate space between pallets for lift truck access can prevent dangerous, costly accidents.
2. Slips, Trips and Falls: Although the easiest to prevent, this segment constitutes the majority of general industry accidents, causing 15% of accidental deaths (2nd to motor vehicle fatalities). Clear, clutter-free work areas, unobstructed aisles/walkways where hazards are quickly cleaned/quarantined, and proper lighting are key to mitigating risk.
3. Hazmat Incidents: Both small and large-scale hazardous material spills threaten worker safety. Here, employee knowledge of proper cleanup and containment procedures leading to the speedy resolution of spills are key, as is access to the proper personal protective equipment and current safety data sheets.
4. Forklift Crashes: Both environmental hazards and operator mishaps contribute to fatal forklift accidents. Proper training on warehouse equipment, inspecting machinery prior to use, knowledge of industry-specific standards, as well as selecting machinery that is easy to use can reduce the risk of forklift-related injuries and deaths.
Move beyond the basics, minimizing employee risk. Boost employee safety and productivity with the latest in warehouse equipment from DJ Products today.