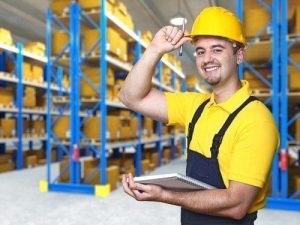
Damages to warehouse equipment are easily resolved by repair or replacement, resulting in a fixed cost. But workplace injuries create a financial ripple effect that goes well beyond medical expenses.
Data shows the average work-related injury costs $188,000, with $150,000 of that amount coming from indirect costs. Here’s a look at some eye-opening facts about warehouse and forklift accidents and the different ways they impact operations.
Causes of Warehouse and Forklift Accidents
– The three most common warehouse injuries result from slip-and-fall; musculoskeletal activities such as pushing and lifting; and use of forklifts and other material handling equipment.
– Most accidents occur in, on or around docks, forklifts, conveyors, material storage and manual lifting and handling.
– Approximately 20,000 workplace injuries are sustained in forklift accidents, with 25 percent resulting from an overturned forklift.
– An average of 100 forklift accidents each year end in fatalities. Roughly 42 percent occur when the operator is crushed by a falling vehicle. In many cases, the seatbelt was not used as per OSHA regulations.
– Pallet jack failure is most often caused by poor work habits such as overloaded or improperly configured racks and operator error.
Employer Costs
Primary direct costs of workplace accidents are medical expenses for the injured employee and repair or replacement of damaged warehouse equipment. Indirect expenses include salaries of temporary workers, changes to insurance premiums, legal costs and lost productivity and business opportunities.
Employee Costs
Injured employees also incur direct and indirect costs. These can include reduction or loss of salary, overtime pay and savings; unreimbursed medical expenses; and ongoing treatment for chronic pain.
Warehouse Equipment Designed for Safety
Our battery-powered warehouse equipment reduces the risk of musculoskeletal injury incurred by handling heavy or awkward loads. Contact DJ Products for more information.