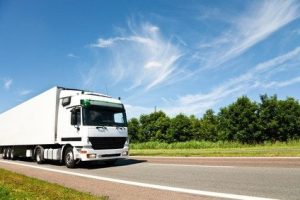
Weigh stations are used to calculate taxes on freight and also to ensure that trucks are below a maximum weight rating. In the U.S., trucks cannot weigh more than 80,000 pounds, and local areas may have lower limits.
Taxing by weight largely eliminates the need for time-consuming inspections. Our powered trailer mover can handle up to 100,000 pounds, but you’d better lighten the load before you drive up to the weigh station!
Truck Weigh Station Methods
Now, about how truck weigh stations work. It’s a lot different than a bathroom scale. Truck scales may be underground or inside of pads, but they all use one of these methods:
– Load-cell systems embedded with wires that sense a difference in electrical resistance depending on the weight
– Bending-plate systems that look like rubber or steel pads and have strain gauges inside
– Piezoelectric systems that use conductors to sense changes in voltage caused by the pressure above
Older technology requires the truck to stop several times with each axle on a scale, but it’s more common to see large scales that look like little landline strips and only require one stop.
As most drivers have noticed by now, there are also “weigh-in-motion” scales that don’t require truckers to stop. Simple versions are pads that truckers can slowly drive over, while more sophisticated technology allows for weigh-ins at freeway speeds.
Tow Trailers Up to 100,000 Pounds
Need a better solution for towing semi-trailers to the dock? DJ Products has beefed up our popular TrailerCaddy to operate as a powered trailer mover that can handle tank trailers, reefers, and even shipping containers.
Save time, improve safety, and avoid the high costs of shunting trucks with a powered trailer mover from DJ Products. Contact us for details.