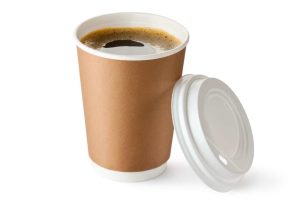
Sleep has no substitute, but coffee really does help you drive safely. Long-haul drivers can focus better and reduce errors with the help of caffeine. Those prone to swerving out of lane should consider a caffeinated chewing gum or cup of joe every few hours.
Worker safety in warehousing and transportation has become a publicized issue lately. Distribution companies should consider all their options for improvement, including motorized trailer dollies for the shunting yard and driver education to reduce accidents.
Coffee Fights Cognitive Fatigue
In addition to keeping you awake, caffeine also produces an adrenaline response that helps with focus. Brain fatigue makes hours of driving feel so tedious. Coffee counteracts that feeling so truckers can have an easier time maintaining a consistent speed, checking their mirrors, and staying in control of the vehicle.
Hit the Road with Caffeinated Chewing Gum
Studies have found the best results with caffeinated gum. The effect kicks in faster and lasts for a predictable 90 minutes. Drinking coffee has less reliable effects (not to mention the associated pit stops).
Trailer Dollies Also Improve Safety
With so much emphasis on driver fatigue and safety protocols, it’s easy to forget that safety starts at the terminal. Drivers and warehouse workers often get injured at the dock while loading or moving trailers.
Replace your shunt trucks with motorized trailer dollies for better sight lines and more precise steering. Any worker can operate a TrailerCaddy, so your truck drivers can save their physical and mental energy for the road—after they’ve caffeinated of course.
Read up on the safety features of our motorized trailer dollies and call 800-686-2651 to speak with a sales engineer about how DJ Products yard trucks can make it very inexpensive to increase workplace safety.