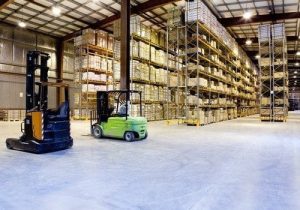
Your warehouse is a vital part of the supply chain. It is imperative that products move through the process efficiently and safely. Accidents can result in damaged products, costly downtime, and injuries or death for your team members. Take some time to review these four common safety problems and take the necessary steps to prevent them in your warehouse.
Insufficient training
Health and Safety Magazine says in depth operator training on all material handling procedures and proper communication of all rules for workplace safety are the most important things all warehouse managers can do to maintain a safe warehouse.
Warehouse ergonomics
Working in the same environment day after day with ongoing pressure to meet tight schedules, it is easy for employees to take their personal safety and things like proper lifting techniques for granted. That is why we offer a full line of ergonomic electric tuggers, powered carts and pullers for any industrial application.
Trips and falls
These common injuries are often the result of fatigue or insufficient sleep. Train your employees to use proper equipment like powered carts when applicable and be sure supervisors watch for signs that workers may be distracted or impaired on the job.
Harmful substances
Some chemicals are necessary, but can also be serious workplace hazards. Be vigilant about safety training and proper handling of harmful substances.
Knowledge of warehouse ergonomics is essential to prevent injuries due to overexertion. At DJ Products, we specialize in providing you with reliable and easy-to-use methods of moving product and heavy equipment. Visit our website for our full line of cart pullers and other warehouse equipment.