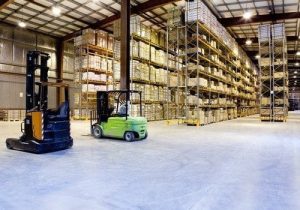
Every warehouse runs as effectively as possible. Orders come in, they get filled and go out. It’s the nature of the business. However, by using a few simple tips you can greatly increase the efficiency of your warehouse, saving time and effort.
- Slot your products by season — In many cases, the usage of certain products depends upon the season. Instead of searching the entire warehouse for seasonal products, group them together so you’ll know exactly where to go.
- Use software for categorization — List the most frequently requested products that you have with software. Instead of endlessly searching the entire database, these products will come up first and limit your search times.
- Group the most requested products together — You can make a warehouse within a warehouse by grouping the most commonly requested products together. Those products which are requested between 70% to 80% of the time, should have their own space. Ideally, they should be closer to the front to reduce travel time.
- Waist to shoulder zone — All of your most commonly requested products, regardless of how you categorize them, should be in the waist to shoulder picking zone. Constantly climbing or bending for the most often requested products wastes time and energy.
- Use the right warehouse equipment — Regardless of anything else, the right warehouse equipment for slotting, picking and moving surplus will improve effectiveness and efficiency in every warehouse environment.
For more information on warehouse equipment for any job, contact DJ Products, makers of trailer movers, dumpster movers and even rail car movers. We have the mobile solutions for all of warehouse floor management needs.