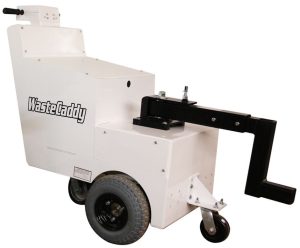
Even though they perform an important function, dumpsters don’t get much love. They provide a convenient disposal location for office and apartment buildings, malls and construction sites, but for most people they’re barely an afterthought. Would you feel differently about a dumpster as a housing option?
A photographer in San Francisco recently used this humorous concept to make a serious point. Fed up with exorbitant real estates prices in his home town, he published a series of tongue-in-cheek photos of “alternative” housing such as mailboxes and manholes covers. The picture of a dumpster was accompanied with a caption referring to it as a “$5,000 waterfront condo”.
All joking aside, without dumpsters trash disposal and recycling would be nearly impossible. The downside is that their size makes them difficult to move, especially when they’re full. Our WasteCaddy and WasteCaddyLite offer perfect solutions to this workplace problem.
These battery-powered pullers are so powerful that one person can easily use them to move dumpsters from underground garages and across dirt and gravel. Their compact design makes them maneuverable even in narrow, confined spaces. Ergonomic features such as the variable speed twist grip help to reduce occurrences of repetitive stress injuries. We also offer a variety of add-ons so you can tailor the caddy to meet your specific needs.
The WasteCaddyLite can handle loads up to 2,000 pounds while the WasteCaddy accommodates up to 5,000 pounds. Our friendly Sales Engineers at DJ Products are ready to help you choose the one that’s right for your application. Please contact us at 800.686.2651 or visit our website to use our convenient real-time chat assistance.