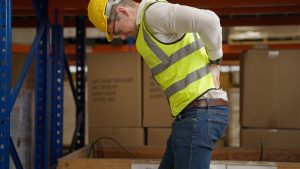
Best Practices for Implementing Ergonomic Solutions in Your Warehouse
Realizing the tangible benefits of ergonomic solutions requires a strategic, multifaceted approach. Here’s how to transform your warehouse into an ergonomic utopia:
Conduct Ergonomic Assessments
Start with a comprehensive evaluation of your workspace and work processes. Gather data on injury rates, employee feedback, and the physical demands of each task. This will help you identify problem areas and prioritize where ergonomic changes are most needed.
Involve Your Employees
No one understands the day-to-day challenges of warehouse work better than the employees themselves. Engage them in the process of identifying and resolving ergonomic issues. Their insights can be invaluable in finding practical and effective solutions. Review the solutions DJ Products offers for the warehouse environment and purchase the “right” tools for the “right” need.
Invest in Training and Culture
Ergonomics should not be an afterthought. Empower your team with the knowledge of safe work practices and foster a culture where ergonomic considerations are integrated into every task and decision.
Regular Maintenance and Upkeep
Ergonomic equipment is only effective when it’s functioning properly. Develop a maintenance schedule to ensure that all tools and equipment continue to provide the support and comfort your employees need.
Remain Adaptive to Change
The nature of warehouse work is dynamic, with new products, processes, and technologies constantly emerging. Your ergonomic approach must be flexible to accommodate these changes and advancements.
Future Trends in Ergonomics for Warehouse Equipment and Operations
The world of warehouse ergonomics is evolving, incorporating cutting-edge technology and new philosophies. Here are some trends on the horizon:
Automation and Robotics
The rise of automation in warehouses introduces a new set of ergonomic considerations. While robots can handle the most strenuous tasks, their interaction with human workers must be carefully managed to prevent new forms of ergonomic hazards.
Wearable Technology
From exoskeletons that support heavy lifting to smart glasses that optimize picking processes, wearable technology is set to revolutionize how workers interact with their environment in ergonomically sound ways.
Big Data and Analytics
Leveraging big data can provide unprecedented insight into the health and safety of your workforce. By analyzing patterns and risk factors, you can fine-tune your ergonomic strategies for maximum impact.
Sustainable Ergonomics
The concept of sustainable ergonomics goes beyond physical health to consider the long-term psychological well-being of employees. This approach focuses on creating work environments that foster engagement, motivation, and career satisfaction.
The Role of Ergonomics in Enhancing Safety and Efficiency in Warehousing
Ergonomics isn’t a single solution but a mindset that should permeate every aspect of warehouse operations. By prioritizing the comfort and health of your workforce, you set the stage for safer, more efficient, and more profitable operations.
Your Path to Better Warehouse Ergonomics Starts with DJ Products
Ready to elevate your warehouse’s ergonomics? DJ Products is at the forefront of ergonomic solutions for warehouses across the globe. Visit our website to explore our range of ergonomic warehouse equipment and learn more about the positive impact it can have on your business and your employees.