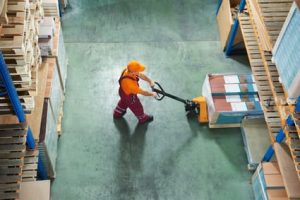
In order to stay competitive and counteract flat sales, supply chain executives are being tasked with reducing labor costs while customers are ordering more frequently in smaller quantities. State-of-the-art material handling equipment is a start, but what’s the rest of the solution?
How to Maximize Order Picking Productivity
A majority of your workforce is involved in order picking, so that’s a logical place to look for areas of improvement. Here are some valuable tips for improving order picking efficiency.
One SKU per Pick Location
Each SKU should have its own individual pick location. The importance of this principle can’t be overstated. Studies show that multiple SKUs at one location can add 15 seconds per transaction.
Some warehouses slot as many as 10 SKUs in one bin location. Not only does this practice add time to the order picking process, it increases the chances of mispicks.
Implement Batch and Cluster Processes
At least half the time of an order picking job is spent in travel. With the average order coming in smaller quantities, this is a perfect opportunity to combine multiple orders that can be completed in a single pick cycle.
Pick Horizontally, Not Vertically
It’s a time-tested fact that it costs more to pick vertically than horizontally. Ideally, all pick facings should be at ground level.
Are you constrained by the dimensions of your warehouse? Wherever possible, slot the highest-velocity items at ground level and proceed vertically from lowest to highest.
Optimize Labor with Material Handling Equipment from DJ Products
Inferior material handling equipment in the warehouse can reduce both productivity and employee morale. Our best-selling CartCaddyLite and other electric tugs, pushers and movers are like adding another worker to the team.
Call 800.686.2651 for more information.