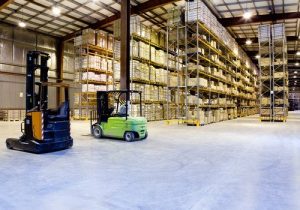
How much loss can you absorb from shipping damage? Getting to zero might be an impossible task, but it’s worth making every effort to reduce the risks. Air bags and strong tape help, but everyone along the supply chain needs the right warehouse equipment and plenty of knowledge for how to prevent product loss.
Reduce Freight Claims, Boost Profit
By using powered warehouse carts from DJ Products, your staff can better manage inventory and load shipments onto trucks and trailers. From a motorized cart pusher to more specialized warehouse equipment like the PartsCaddy or CarpetCaddy, there’s a tool for every job.
Logistics experts recommend taking even more action to prevent shipment damage:
– Test shipment methods before rolling out a new product
– Cube stacks of boxes to prevent damage during transit
– Train workers on proper use of box-cutters
– Apply shock and tilt indicators to fragile packages
– Make customer return supplies easy to use
Focus on What You Can Control
Whichever leg of the supply chain your company handles, there are many factors out of your control. From the factory to the last-mile delivery service, many hands touch each package. To prevent damage from shipping, focus on your own warehouse equipment and identify the places and situations that can cause damage.
Crushed box corners and shattered products are signs that employees might be overwhelmed at the warehouse. Does your team have the right material handling equipment for the weight, size, and volume of packages they handle?
DJ Products offers powered cart pushers and tugs for loads ranging from 1,500 pounds to 50,000 pounds. For every application, we have warehouse equipment that can save time, prevent worker injury, and make it easier to deliver the goods intact. Contact us for more info.