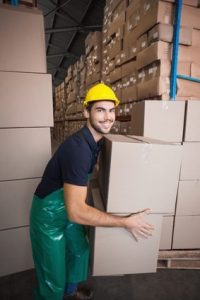
Warehousing and storage may not sound like a particularly risky industry. But in fact, according to the Bureau of Labor Statistics, workers in this segment suffer musculoskeletal injuries twice as frequently as those in general private industry.
Improve workplace safety and reduce injuries by implementing sound ergonomic principles for the more common physical tasks.
Placing and Picking
• Teach proper body alignment so employees aren’t forced to twist their back.
• If possible, organize the workplace so employees don’t have to reach up or bend down to perform activities.
• Use a dumpster puller or other battery-powered mover for heavy loads.
Packing
• Make sure employees maintain a neutral posture: straight neck and back, shoulders down, elbows at right angles, wrists straight.
• Minimize the need to apply force such as pinching, pushing, pulling or gripping.
• Use carts and conveyors to reduce manual movement of items.
Shipping and Receiving
• Enforce proper lifting techniques to engage knees and legs rather than the back.
• Use mechanical assistance whenever possible.
• Keep loads in the zone between knees and shoulders. Particularly heavy loads should be between knuckle and elbow height.
Boost Workplace Safety with a Dumpster Puller from DJ Products
Surprisingly, the trash room is the most dangerous spot in a workplace. Injury risks range from overexertion due to moving heavy loads to pinching fingers and hands in dumpster lids.
Satisfied customers say that our WasteCaddy is “like having another employee on staff.” A single employee of any age or size can perform an activity that usually requires two workers.
Call 800.686.2651 to get cheerful assistance from one of our knowledgeable sales engineers.