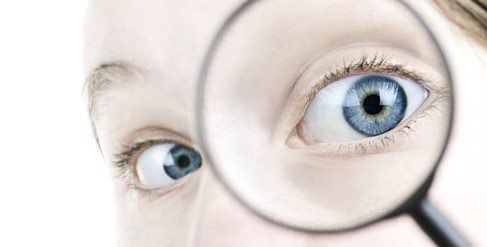
The 2016 Defense Authorization bill initiated a process of streamlining the DoD acquisition system by moving power into the hands of military service chiefs and secretaries. Congress recently agreed on the 2017 bill, which continues the reform aimed at encouraging more commercial buying.
Removing the Roadblocks to Commercial Acquisition
According to Bill Greenwalt, a Senior Senate Armed Services committee staffer, the shift toward commercial purchasing occurred 20 years ago, but the system was less agile than it was hoped. Leaders of the Defense committees hope to take advantage of the high level of innovation occurring in the commercial sector.
Greenwalt goes on to explain that, while Part 12 of the Federal Acquisition Regulation grants the DoD authority to purchase from commercial companies, it was laden with clauses that made it difficult to do so. Such regulations are actually meant to cover acquisition of major weapons systems.
New Pilot Program for 2017
The preference for commercial contractors extends to services including construction, medical and transportation as well as products. The new bill also mandates a new pilot program allowing the DoD to bypass requests for proposals for purchases of “innovative commercial items” up to $100 million in favor of open calls to industry.
Industrial Tugs for Defense Contractors from DJ Products
Reduce expenses and save manpower with our comprehensive line of battery-powered industrial tugs for defense contractors. A single employee using these tugs can maneuver boats, aircraft, missiles and other heavy equipment with ease. Use the handy chat feature on our website and let our friendly sales engineers help you select the right option for your application.