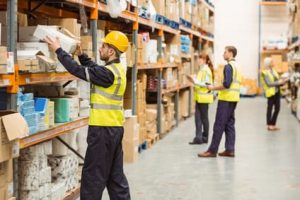
How can your warehouse keep up with the challenges of today’s increasingly competitive industry? Use labor-saving solutions from a material handling equipment supplier and integrate Internet of Things (IoT) technology for state-of-the-art warehouse management.
IoT Applications for Warehouses and Distribution Centers
Business technology has gone far beyond consumer applications. The IoT provides efficient and accurate ways to manage even the most complex warehouses through every step of operations.
– Products can be located at each point in the supply chain through unique ID numbers.
– Real-time data collection allows for speedier and more effective decision making.
– Data sharing across platforms and between departments is simplified.
– Detailed information can be attached to all incoming and outgoing transactions without the need for human interaction.
– Patterns can be identified and used to improve speed, accuracy and efficiency.
– Reporting, alerts and notifications are available through a number of devices.
Continuing Benefits of IoT-Equipped Warehouses
Currently, 10 percent of companies have implemented IoT systems, while another 30 percent are planning to adopt the technology. Over the next 10 years, the IoT industry is predicted to reach a global value of $8 trillion.
Companies are increasingly viewing warehouses as value streams rather than merely inventory storage. IoT systems can help create leaner systems by reducing wasted time, labor and supplies. As a result, both vendors and customers will have higher levels of confidence and satisfaction.
DJ Products: Your Complete Material Handling Equipment Supplier
Overexertion due to lifting, pulling, pushing and carrying is the number one cause of workplace injuries. We offer a comprehensive line of battery-powered pushers, tugs and movers to fit any material handling application.
Visit our website and use the convenient online chat feature for immediate assistance from our friendly and knowledgeable sales engineers.