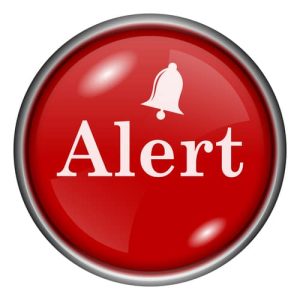
While the e-commerce boom has caused a major spike in demand for warehouse space, competition has come from an unlikely source. Marijuana startups in cannabis-friendly cities such as Denver and Seattle are driving industrial rent prices sky-high.
Marijuana Industry: A Boon for Industrial Landlords
CoStar Group Inc., a research firm that tracks data on commercial properties, found that warehouse rents in Denver, Seattle and Portland rose 27 to 33 percent over the last three years, compared to 19 percent in other markets. Similar results are expected in Los Angeles, Boston and Las Vegas now that these areas have legalized recreational marijuana use.
“Ganjapreneurship” has also caused a corresponding reduction in vacancy rates. Weed sellers tend to choose smaller, less desirable buildings where it’s easier to control the fire risks that accompany the cultivation of marijuana.
Although marijuana has been legalized in these areas, the industry still carries a stigma due to the federal ban. As a result, landlords are asking for, and receiving, higher rent rates.
No End in Sight
In 2016, cannabis sales exceeded $6 billion. Thanks to the recent legalizations, one in five adults will now live in an area that permits recreational weed. Add the expected development of online pot sales, and it’s clear that the demand for warehouse space won’t be relaxing anytime soon.
State-of-the-Art Warehouse Equipment Movers from DJ Products
No matter what products are stored in a warehouse, streamlined operations are essential to maximizing productivity and reducing expenses. Visit our website to learn more about our CartCaddy5WP and other battery-powered warehouse equipment tugs, pushers and movers.