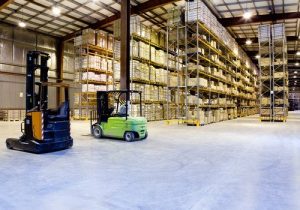
In the trucking industry, nothing is worse than a disorganized warehouse. It can really slow down your company’s daily operations and put you dangerously behind schedule. But the good news is that there are ways to remedy this.
The right material handling equipment can help you in more ways than you probably realize. We’d like to offer some helpful organization tips that you can put to use right away.
Tips for Organizing Your Warehouse
Keeping your warehouse organized doesn’t have to be difficult. In fact, by making a few simple changes you’ll notice that your daily operations will run much more smoothly.
Tip #1: Label everything. It might seem like you’re taking an extra step, but really, labeling everything as it comes through the door will save you a lot of time and frustration in the long run.
Tip #2: Keep any high velocity items in easy to reach places. This will help your workers stay more efficient and you’ll be much more likely to get orders out on time.
Tip #3: Finish all orders before the shift ends. It’s way too easy for orders to get lost or forgotten during shift changes. Make sure your workers have the time they need to get them all finished.
Tip #4: Implement regular cycle counts instead of waiting to do inventory at the end of the year. This one step can change everything for your business. You’ll be able to stay on top of any problems.
Tip# 5: Resolve to use the best in material handling equipment to keep things running efficiently. You might not know exactly what you need, but we can help you at DJ Products.
The best time to get organized is right now. Contact us for assistance!