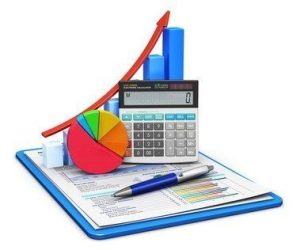
Do you have the right material handling equipment to keep up with industry changes? MES (Manufacturing Execution Systems) and WMS (Warehouse Management Systems) are merging. To meet changing operations, such as warehouses taking on manufacturing roles, tighter/leaner order requirements and ever-faster shipping expectations, new trends are emerging, syncing WMS and MES to allow for real-time knowledge of materials flow and finished goods status.
Smaller, More Frequent Work in Progress (WIP) Replenishment
Instead of large production runs and big loads, e-commerce bigwigs are trending toward smaller production runs and more frequent replacement. Since MES governs production, and WMS governs inventory/material movement, these two systems must work in synchronization to ensure accurate inventory levels and safeguard shipping times.
More Value-Added Services
WMS vendors are moving toward increased manufacturing/customization capabilities, completing assembly/customization with key components which are later assembled in manufacturing areas of warehouses. Here, the synchronization of WMS and MES are key, ensuring ‘just in time’ (JIT) replenishment by supplying a dynamic ‘shopping list’ of what needs to move into assembly centers, and when. This JIT replacement cuts WIP inventory space on the warehouse floor as much as 95%, dramatically streamlining operations.
Integrating WCS with WMS
Integrating WMS with Warehouse Control System software, which controls automated materials handling equipment, offers access to real-time data from automation processes. This facilitates material movements into/out-of manufacturing work centers, prevents disruptions/bottlenecks, identifies them, adjusts the movement of material to adapt to the situation, and prevents (and potentially predicts) further issues.
Increased Use of Robotics
The integration of WMS and MES can also help users more precisely manage fleets of autonomous mobile robots, fine-tuning operations and optimizing routes from storage to shipment.
What’s moving your business? Find the material handling equipment you need at DJ Products today.