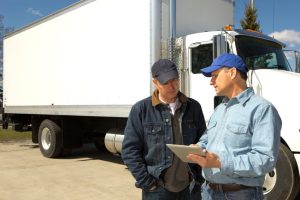
As a warehouse manager, you can improve productivity and employee morale by being proactive about safety. Upgrade working conditions by using warehouse tugs and implementing this checklist of safety practices.
1. Create a Culture of Safety
Establish a shared concern for safety among employees. Set mandatory standards and communicate expectations through verbal and visual reminders, including safety tips posted in appropriate areas.
2. Review Workplace Conditions
Maintaining a safe workplace is an ongoing job. Conduct regular walk-throughs of the warehouse with an eye out for blocked aisles, exposed electrical cords and other common safety hazards.
3. Hold Training Sessions
Schedule periodic training to reinforce safety behavior and update employees on current regulations. Encourage questions and discussions and give occasional pop quizzes to keep awareness high.
4. Recognize and Reward Safety Practices
Recognition is always an effective way to internalize behavior. Start a program that allows employees to nominate co-workers who have demonstrated excellent safety practices and provide rewards.
5. Establish a Safety Committee
Involve employees directly by creating a safety committee that empowers them to take responsibility. Members can take questions and concerns from other workers, follow through on solving problems, and taking charge of training programs.
6. Have Clear Emergency Procedures
Provide first-aid kits, fire extinguishers and other emergency safety equipment and make sure everyone knows where they’re located. Emergency exits should be clearly marked and all employees should know the protocol for evacuation in case of fire or other dangerous situations.
Warehouse Tugs: An Effective Solution for Workplace Safety
Electric warehouse tugs from DJ Products include a wide range of safety features to reduce the risk of workplace accidents and repetitive-use injuries. Visit our website and learn more about our full line of material handling equipment.