This post is a continuation of Part One found on our blog.
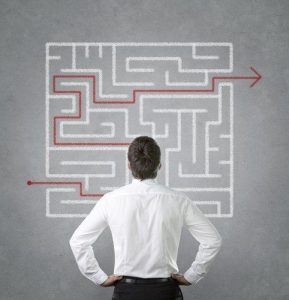
We brought in the new year with a look at supply chain trends that are expected to affect the industry in 2018 and beyond. While tugger carts and other electric material handling equipment are established parts of today’s warehouses, we continue to examine developing factors that can change your approach to workplace operations.
Emphasis on Supply Chain Externals
As environmental awareness has continued to grow, the public has become more concerned about how companies affect society in terms of carbon footprint and sustainable practices. Companies will need to increase transparency with disclosure of the end-to-end impacts of supply chains.
Serving the “Base of the Pyramid”
More than five billion people around the world make less than $2,000 per year. An influential book entitled The Fortune at the Bottom of the Pyramid explored the market potential of this segment. As a result, current cost-plus supply chain models will transition to not-to-exceed cost models.
Global Demand for Knowledge Work and Workers
The shift to a global market has increased the need for supply chain workers who understand the local complexities of foreign communities and have an ability to communicate in multiple languages. Approximately 40 percent of this work involves analytics, planning and processing.
Identifying Micro Segments
Supply chain usually paints the model of customer service with a broad brush that addresses the basic category. Companies are now finding more success with a supply chain that effectively serves specific micro segments of customers based on what triggers their buying decisions.
Increase Safety and Productivity with Tugger Carts from DJ Products
Our electric tugger carts provide a consistent level of safety and efficiency that maximizes productivity in your workplace. Visit our website to learn more about our full line of material handling solutions.