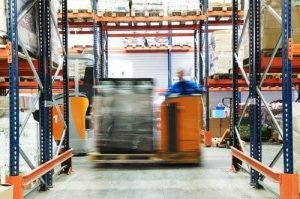
Good housekeeping shouldn’t be confined to your place of residence. Maintaining a tidy workplace and using tugger carts reduce injury risk and promote high levels of efficiency.
Incorporate these expert tips for making cleanliness an important part of your workplace culture.
Prevent Slips-and-Falls
Slips, trips and falls are second only to musculoskeletal stress as a cause of workplace injuries.
– Keep aisles and doorways free of obstructions.
– Clean up spills and leaks as soon as they occur.
– Immediately repair or replace worn-out or damaged flooring.
– Use strategically placed floor mats to provide traction and prevent employees from tracking materials across the warehouse.
Control Dust
A layer of dust no thicker than a dime presents a serious explosion risk. Use vacuums and compressed air to keep all surfaces, materials and equipment dust-free.
Remove Clutter
Clutter forces employees to restrict their movements, which can lead to sprains, cuts and other injuries. Make it a habit to return items to their proper place after use and keep extraneous items out of the workplace.
Use Personal Protective Equipment
Personal protective equipment such as safety glasses, closed-toed shoes and face masks should be used appropriately, with no exceptions. Have supervisors conduct regular checks to make sure all PPE is in good working condition.
Create and Maintain Written Housekeeping Policies
Create a manual thoroughly detailing housekeeping policies and keep it updated. All employees should be trained on proper procedures and have convenient access to the manual.
Save Time and Money with Tugger Carts from DJ Products
Our battery-powered tugger carts pay for themselves many times over in improved productivity and reduced workplace injuries. Visit our website and get real-time assistance from our sales engineers to select the perfect tugger carts for your warehouse.