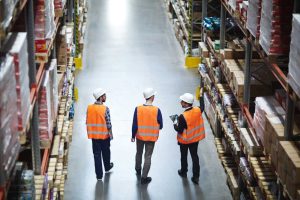
So, you’ve made the decision to implement material handling tugs in your warehouse to protect workers and improve productivity. How do you decide which ones are best for your applications? Our experts share five questions that will help you choose.
1. Does the tug promote a safe working environment?
A good tug allows a single employee to easily move heavy objects and materials with less effort. In addition to strength, the tug should offer maneuverability through tight quarters that will reduce the risk of collisions, falling containers and other mishaps.
2. Does the tug cut down on physical strain?
Transporting bulky or heavy items often results in workers twisting, turning and bending, which can lead to injuries as well as chronic pain in the long term. With our tugs, once the connection is made, a worker simply walks at a normal pace to operate it.
3. Does the tug promote proper posture?
When employees contort their bodies into awkward positions to move heavy objects, it places excessive stress on their musculoskeletal system. While it may get the job done, workers pay the price in sprained muscles and damaged joints. Operating our tugs lets employees maintain a neutral upright position that avoids strain.
4. Does the tug minimize the need for manual tasks?
Manual material handling, or MMH, is a frequent cause of back pain and overall fatigue. Statistics indicate that three-quarters of workers involved in MMH tasks experience injuries that make up one-third of compensation costs. Quality material handling tugs take the burden from workers, safeguarding their well-being.
5. Is the tug ergonomically designed?
Repetitive motions can often lead to long-term physical problems. A tug that’s ergonomically designed includes features that reduce wear and tear from these movements. It also creates a safe grip to optimize control and reduce the risk of accidents.
Choose Electric Material Handling Tugs from DJ Products
Our comprehensive line of battery-powered tugs, movers and pushers make warehouse safety a priority while also reducing your carbon footprint. Contact us at 800.686.2651 or use our handy online chat feature, where our knowledgeable Sales Engineers are ready to answer your questions.