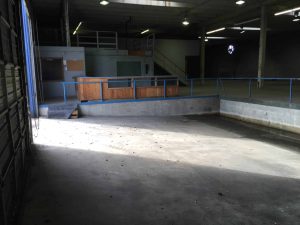
The U.S. Labor Department estimates that the number of retail jobs lost over the past 17 years is the same as the number of new hires by online retailers like Amazon. That staggering number is approximately 444,000 people. The e-commerce industry toppled retail by providing a new kind of customer convenience and by maximizing manpower with warehouse equipment to quickly move high volumes of products through the system.
The labor market changes
In past years, retail workers were spread across the country at brick and mortar stores. Currently, an increasing number of shoppers have opted to do more of their shopping online. This has resulted in huge warehouses located in a small number of strategic locations that need workers to fulfill customer orders.
Although President Obama and President Trump have bemoaned Amazon eliminating traditional retail jobs, a recent DallasNews article reports the e-commerce industry is adding more jobs than the retail sector is losing. For many people previously employed in face-to-face retail, the pay, benefits, and working conditions are better in the warehouse industry.
Some previous retail workers are still struggling
With e-commerce, the warehouse industry now provides some markets with plenty of available jobs with good pay. Amazon warehouses are clustered near a relatively small number of Amazon facilities, which leaves some displaced retail workers struggling to find work. Online retailers still rely on people with jobs purchasing goods for revenue. Where and how the U.S. economy finds a balance for the e-commerce revolution is not entirely clear.
At DJ Products, our mission is to provide warehouse equipment to help businesses operate more efficiently and prevent injuries to warehouse staff. Contact us today to speak with one of our helpful sales engineers about our full line of products.