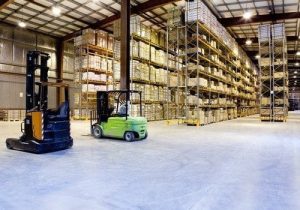
Savvy consumers and a fiercely competitive marketplace have created a demand for condensed delivery schedules, with buyers thinking in terms of days instead of weeks. As a result, companies are using new strategies to streamline putaway and storage functions.
Have you implemented any of these procedures in your warehouse?
Crossdocking
Crossdocking involves moving product directly from the inbound dock to an outbound trailer without putting it in your physical inventory. This process frees up warehouse space while reducing the amount of handling required. In order to realize maximize benefits, appropriate systems should be installed.
Pre-Allocation
Instead of storing products in different warehouse areas or even different DCs based on distribution channels, companies are using one common inventory. Products are then pre-allocated and batched ahead of time to allow for different value-added services.
Supplementing with Automation
Labor is a major expense, and competition for manpower presents a challenge in finding skilled workers. Companies are augmenting their workforces with automated storage and retrieval solutions to improve efficiency and control labor costs.
Single Locations
Sometimes old-school techniques are still relevant. With e-commerce creating the need to maintain increasing numbers of SKUs, placing a single carton in a single location makes it easier for employees to quickly access specific products.
Save Time and Labor with Warehouse Tugs from DJ Products
Minimize material handling time with our battery-powered warehouse tugs. Ergonomically designed pushers like our CartCaddy5WP enable a single employee to smoothly and efficiently transport and maneuver loads up to 10,000 pounds. Call 800.686.2651 and let our friendly sales engineers help you find the best solution for your company’s needs.