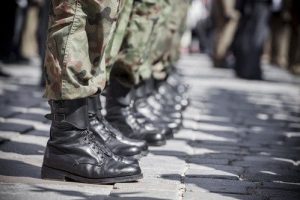
In January 2016, the Department of Defense instituted a policy aimed at streamlining their services contracting with better oversight and control. While the new policy is expected to make the process more cohesive, it may take another dozen years before coming to full fruition.
“A 15-Year Effort”
More than half of the Department’s procurement budget is allocated to services, with the remainder for purchases such as contract equipment. According to Ken Brennan, deputy director of services acquisition, the goal is for contracts to become part of “the general culture and policy” rather than standalones.
In Brennan’s view, the new policy is “a 15-year effort” that is already about three years along. Brennan adds that is making significant progress, and he anticipates potential for guidance soon in the areas of small businesses and administrative services.
Functional Domain Experts
One major change involves the creation of functional domain experts, or FDEs, to lead each of the individual service sectors. Claire Grady, director of defense procurement and acquisition strategy, explains that this lets people with particular expertise create strategies to improve planning and execution while reducing costs.
FDEs will also implement metrics to monitor contract performance, determine best practices and recommend policies. Grady says will be paying close attention to the metrics established by these new domain leaders.
Military and Material Handling Solutions
DJ Products offers quality options for contract equipment. Our battery-powered tugs and movers handle applications like maneuvering aircraft in and out of hangars and pulling heavy engines and parts. Visit our website to have your questions answered online by one of our knowledgeable sales engineers.