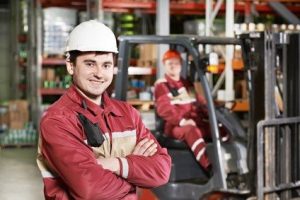
Robotics, in combination with warehouse equipment, has become a dynamic means of boosting productivity with lower costs. Exoskeleton robots are now poised to become the next big innovation in supply chain and logistics.
Could exoskeleton robots have an application in your warehouse operations? Here’s what you should know about this fascinating technology.
What Are Exoskeleton Robots?
Exoskeleton robots are wearable devices that incorporate electric motors, pneumatics and hydraulics to mimic or augment actual human movements. These devices afford a greater degree of strength and endurance than workers could achieve on their own.
Applications of exoskeleton robots cut across a wide range of fields, from manufacturing and supply chain to healthcare and military. As a result, the market is expected to reach an astonishing $2.8 billion by the year 2023, for a compound annual growth rate of 45.2 percent.
Advantages of Exoskeleton Robot Use
Muscle fatigue and overuse is a primary limitation in a number of activities. An exoskeleton robot lets the user remain functional and productive beyond the point at which they would normally have to stop.
Exoskeleton robots are currently incorporated extensively in two industries:
– Healthcare services use exoskeletons for injury rehabilitation to help muscles recover efficiently.
– The military uses exoskeletons in combat situations to reduce fatigue and injury risk among soldiers.
Full-body exoskeletons aren’t yet ready to be rolled out commercially, but upper- and lower-body exoskeletons have great potential as ergonomic aids for warehouse workers who perform repetitive tasks.
Make Safety a Priority with Ergonomically Designed Warehouse Equipment
Battery-powered warehouse equipment like our best-selling CartCaddyShorty includes features such as variable speed twist grips to prevent common repetitive motion injuries. Use our convenient online chat feature to learn more from our helpful sales engineers.