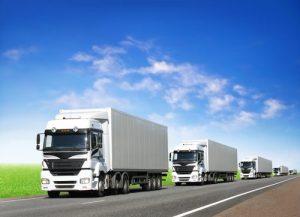
The trucking industry in the United States is more than a century old, yet it continues to change along with the times. Here are some of the major trends that will impact the future of transportation in 2017.
1. More Productive Vendor Relationships
As trucking companies continue to deal with labor shortages and other obstacles, they will rely increasingly on trusted vendors for advice and solutions. Thanks to a varied customer base, vendors get a broad view of the industry and you can benefit from their greater perspective.
2. Greater Integration of Technology
Improving efficiency and profitability is a permanent goal of all trucking companies. GPS and other sophisticated technology provide a valuable advantage in cost-effective measures such as mapping the best routes and planning optimum truckloads.
3. Self-Driving Vehicles
Automation took a huge step forward last year as a San Francisco startup owned by Uber made a delivery of beer to Colorado using a self-driving truck. Odds are slim that the trucking industry will become completely automated, but it’s another new technology that you should evaluate for possible benefits to your company.
4. Changing Regulations
The government is also adapting to the ever-shifting landscape of the transportation industry. Regulations are created, changed and discarded in order to cover worker safety, environmental issues and other pressing concerns, and you can’t afford to fall behind.
Trailer Mover to Pull Semi Trailers from DJ Products
Our battery-powered trailer mover to pull semi trailers is safe, eco-friendly and economic, allowing a single employee to move loads of up to 100,000 pounds. Visit our website to learn more.