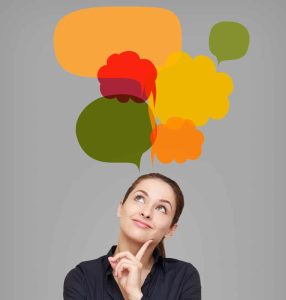
Our battery-powered tugger carts are ergonomically designed to prevent carpal tunnel syndrome and other injuries caused by repetitive motions. How much do you know about ergonomics and the role they play in maintaining a safe warehouse?
Observing ergonomic principles allows workers to be more productive while reducing physical stress. Here’s a look at how you can put ergonomics to work in your warehouse.
What Is Ergonomics?
Ergonomics, sometimes referred to as human engineering, is broadly defined as “the study of the relationship between workers and their environment.” The ultimate goal is to design the workplace for optimum efficiency and less physical wear and tear.
Whenever possible, work motions should be centered around the “golden zone,” which refers to the body’s core between shoulders and knees. Workers should rarely, if ever, have to reach above their shoulders or below their waists.
Types of Ergonomic Injuries
Ergonomic injuries tend to fall under two categories:
– Lifting and handling injuries occur when heavy boxes, pallets and other loads are placed too high or too low.
– Overexertion injuries result from repetitive motions, such as long walks during order-picking.
Ways to Improve Ergonomics
– Slot SKUs appropriately with high-volume items placed close by.
– Install pallet flow racks so a case is ready at the point of pick.
– Use tilted pick trays for items stored higher in the rack.
– Train employees in the proper operation of tugger carts and other equipment.
– Encourage workers to report unsafe conditions or inefficiencies in workflow.
– Prioritize regular housekeeping to eliminate cluttered aisles and other hazards.
Ergonomically Designed Tugger Carts from DJ Products
Electric tugs such as our best-selling CartCaddyShorty reduce the risk of both lifting and handling and overexertion injuries. Visit our website and learn more from our helpful sales engineers.