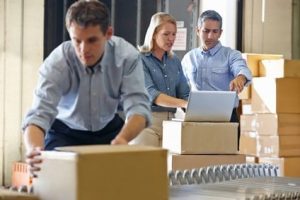
Damaged stock is one of the primary factors reducing warehouse and supply chain profitability. The impact can be direct, as in the case of incomplete orders, or indirect, such as when an accident injures an employee.
Anywhere from two percent to 11 percent of products received are already damaged, but the problem isn’t simply a matter of chance. Experts recommend use of tugger carts as one of the proactive ways to reduce the amount of damaged stock in your warehouse.
Improve Workflows
How is stock typically handled during day-to-day operations in your warehouse? Review the process from start to finish and look for areas of improvement, such as reducing the number of times a case is touched.
Use Material Handling Equipment Whenever Possible
Material handling equipment involves a significant financial investment, but the costs will be more than offset by less product damage and fewer job-related injuries.
Reassess Racking Systems
If the racking system is inadequate, it could result in improper storage which is a leading cause of damaged stock. In addition to upgrading racks, consider installing safety equipment such as column protectors and aisle shields.
Train Employees
Employees are on the front lines when it comes to handling and processing stock. Incorporate product awareness into your ongoing safety training workshops.
Build a Culture of Cleanliness
It sounds simple, but employees sometimes become lax about keeping the warehouse clean, whether it’s due to work deadlines or thoughtlessness. Create and enforce standards of cleanliness and hold employees accountable.
DJ Products Makes Tugger Carts to Solve Any Need
No matter what types of products are handled in your warehouse, we have a wide range of tugger carts to improve safety and productivity. Use our handy online chat feature to learn more.