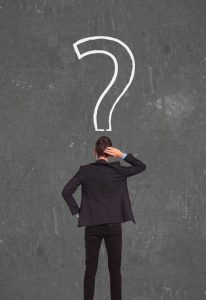
Do you track your workouts with a FitBit or run your household with the help of Amazon’s Alexa? Welcome to the Internet of Things (IoT), a world of “smart” devices that are impacting your personal life and revolutionizing supply chain management.
Making Your Supply Chain “Smarter”
While these Internet-connected devices have been making a big splash, it’s not going to slow down any time soon. In fact, research firm Gartner recently issued a prediction that the number of IoT devices will increase thirty-fold by the year 2020.
How does this new technology impact supply chains and logistics? The IoT will connect people, processes, information and equipment to an extent never before possible, providing an amazing depth and breadth of data.
A Real-Life Scenario
A significant example of this benefit is in-transit visibility. As products pass through a number of points between manufacturer and consumer, an agile supply network is needed to follow them through all steps of the supply chain.
Cloud-based GPS and radio frequency identification (RFID) technologies can be used to transmit identity, location and other data that’s crucial to accurate tracking. With a chip in a pallet and a coordinated device in the shipping vehicle, stakeholders can monitor progress in real time and make proactive decisions based on the constant flow of data.
DJ Products: The Leader in Warehouse Handling Equipment
While the IoT takes supply chain management to another level, our battery-powered warehouse handling equipment makes labor-intensive tasks easier and safer. Contact us to learn more about our popular CartCaddy5WP and other products in our full line of electric pushers, tugs and movers.