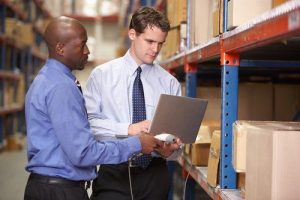
Our rugged warehouse equipment is designed to perform under a wide range of conditions, but it’s not always so easy for people to operate in bad weather. Snow, ice and other treacherous winter conditions can make it dangerous to be on the road.
Use these tips to create a clear and comprehensive snow and bad weather attendance policy that protects employees while minimizing work interruptions.
Know the Law
At a minimum, your policy must meet the parameters set forth in the Fair Labor Standards Act. Rules differ for exempt and non-exempt employees, so set yours accordingly.
Be Consistent with Company Culture
Policies should always reflect company values. Is your culture more traditional or does it embrace flexibility? Whatever your identity is, keep it in mind as you compose the bad weather policy.
Consider All Employees
First of all, many companies have several locations that may require individual policies. Second, even within a common workplace, employees have different considerations such as travel time and mode of transportation. Aim for a policy that encompasses all situations.
Define “Bad Weather”
Everyone has their own perception of what constitutes bad weather. Choose a specific but fair method of triggering the bad weather policy, such as a minimum amount of snowfall or when schools are closed.
Have an Action Plan
A complete bad weather policy should set out precise steps for actions including notifying employees, alerting customers and implementing a virtual office set-up.
Safety Comes First
Regardless of the formal policy, let workers know that you value their safety. Be flexible with issues like start times and dress codes.
Reliable Warehouse Equipment from DJ Products
No matter what the weather is outside, our warehouse equipment is always ready for duty. Contact us for more information.