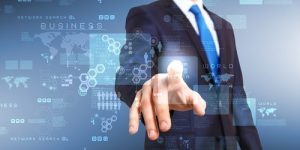
Every year the threat of work-related injuries is disconcerting for the millions of warehouse workers and employers that drive our economy. Tens of billions of dollars are spent by employers annually to address work-related accidents. Technological advances that have been introduced to the business industry are offering life-changing solutions to address mounting safety concerns. It’s easy to open the door to new safer working conditions when robotics plays a key role in bettering your workplace environment and your manufacturing capabilities.
The Best in Material Handling Equipment
Mobile robotic order pickers are quickly becoming the new normal in warehouses. Repetitive motion is a common cause of labor force injuries. Robotic machinery is even now being programmed to organize, pick and move hard-to-reach orders in warehouses across the world. The right robotics can alleviate any excessive strenuous labor your dedicated workforce engages in. At DS Products, we offer the benefits of complex machines to complete tasks that wear on our employees and their physical capacities. Material handling equipment such as these product types below allow enterprising companies to expand production and keep loyal workers from overexertion:
*Bin Pullers
*Aircraft Tow Tugs
*Trailer, Vehicle and Equipment Movers
Running On Robotics
Reaching for packages on high shelves while using ladders or other precarious means can be dangerous. In fact, falls from high places on the job were in the top 10 causes of work injuries. Robotic machinery such as pullers, pushers or various movers is time-saving and allows your employees to expend their energy on more important tasks without the threat of incurring minor or life-altering injuries.
Peruse DJ Products today to find quality material handling equipment that uses technology to counteract safety concerns and unneeded expense.