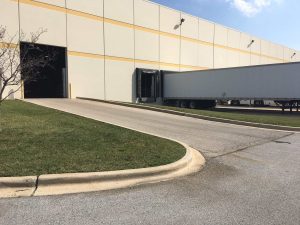
Do your operations grind to a halt whenever a dock suddenly needs critical maintenance? Many dock problems can be prevented with more proactive care, cutting down greatly on the overall costs of your warehousing and logistics facilities, says Modern Materials Handling.
Gary Forger reports that insufficient maintenance accounts for up to 85% of all dock equipment problems. Planned maintenance can prevent much of that while also reducing the frequency of emergency repairs.
Options for Planned Dock Maintenance
Warehousing and logistics managers have multiple options for better planned maintenance:
• Add or appoint an in-house employee
• Partner with dock equipment suppliers to advise in-house staff
• Outsource to a structured dock maintenance program
Tips for Warehouse Dock Maintenance
The first step is to determine how often various components need recommended inspections and maintenance. Some parts need annual care, others should be maintained every 90 days.
In addition to checking for broken or worn-out parts, workers should test for energy leaks that may be costing a fortune.
Keep hydraulics working efficiently with proper fluid levels and lubricate moving parts regularly to prevent small wear-and-tear from becoming major damage or causing a shutdown.
Finally, consider how dock maintenance can improve worker safety. Dock-related injuries are common, resulting in good workers missing days and leading to claims.
On that note, DJ Products has industrial cart movers for the warehousing and logistics industry that can significantly improve your bottom line—through reduced injury risk as well as better productivity. We also have a line of trailer movers for improved safety around dock doors.
Contact DJ Products for more info about material handling solutions for warehousing and logistics.