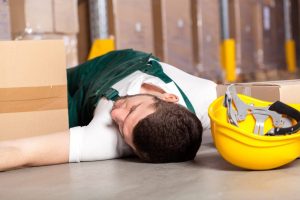
Summer is quickly approaching and with it comes rising temperatures. For warehouse employees who are diligently working inside, summer months are something to dread. Spacious work areas are difficult to warm and extremely expensive to cool. So how can employees and their conscientious employers gain some relief from the heat? Check below for a few easy-smart heat-battling tips!
Prepping for the Heat
Extreme heat conditions are trying on the body in any environment, and especially on the job. In buildings that are vulnerable to intense temperatures, your employees often battle exhaustion, dehydration and other trying ailments related to heat. On the business side, difficult working conditions lower productivity and increase the potential for threatening and costly safety issues. Here are some summer heat solutions you can implement to create better on-the-job experiences for your hard-working base:
– Make sure to inspect the insulation. If the warehouse building is properly insulated, heat can’t find its way in quite as easily.
– Add ceiling fans. They are affordable options that allow for good air flow to permeate large areas.
– Fight humidity. By running dehumidifiers, removed moisture often brings instant cooling relief.
– Inform your workers of heat dangers. Knowledge is an elemental factor in preventing dangerous accidents. Self-awareness plays a part in lessening the chances of incurring injury related to high heat levels.
– Purchase durable material handling equipment. High-functioning material handling equipment performs well in various temperatures. Heat wreaks havoc on machines that run too hot. Hot machinery produces excessive heat. The right products simplify worker tasks rather than create more troublesome problems.
Ensure good working conditions continue by employing the proper preventative procedures. And when you utilize quality material handling equipment like those offered by DJ Products, productivity and employee morale will increase!