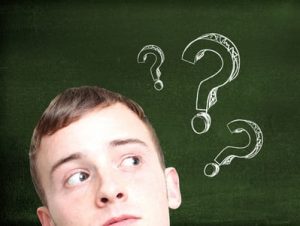
One of the most overlooked warehouse management tips is attracting and keeping young talented workers in a department of defense contractor scenario. This may even seem like a non-issue because the standard has always been to give someone a job, give them a fair rate of pay, and they would then stay there until they retired.
But that mindset no longer works for a modern job force under 30 years of age. You have to learn and understand the nature of this modern workforce in order to keep them on the job for the long haul.
Family Friendly
Although you are employing one single person, the family comes along for the ride. Competitive businesses allow such things as paternity leave, flexible schedules and telecommuting, to name a few. Making your business family friendly makes for long term employment.
Growth Within
In this case, one of the most important warehouse management tips is to give the opportunity for growth within the company. These younger employees are more apt to enroll in higher education, gain knowledge and experience, and move on to another job if a growth opportunity does not present itself within a reasonable time.
Perks
In this day of modern communication, which is nearly constant, get Wi-Fi for computer access to allow these younger employees to stay connected during lunch hour and breaks.
Many employees may also have kids that need daycare or nannies, and that can be a valuable perk if offered on-site.
For more information on this or products that will aid your DOD warehouse, contact DJ Products, makers of trailer movers, tuggers, dumpster movers and aircraft tugs.