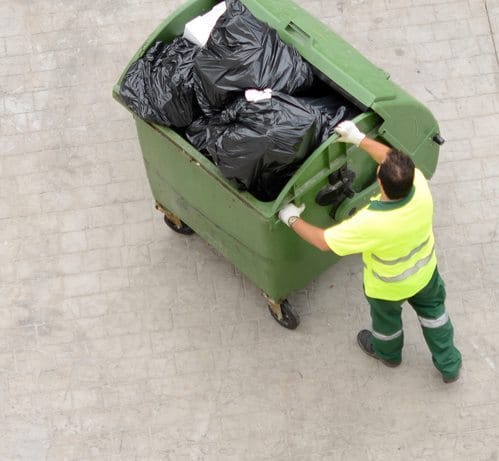
Janitors and maintenance teams have enough physical strain in the course of their job. After making the rounds, lifting and throwing bags into the dumpster and dealing with oversized items, the employee then has to push the waste container to the proper collection site. That last step can be the most difficult – manually pulling or pushing thousands of pounds.
Tips to Prevent Injuries to Maintenance Staff
Prevention has two main components: general health and ergonomics. The ergonomic part is easy – you can switch from manual power to battery-powered waste caddies that motorize the most difficult part of the job.
Safety experts also recommend taking a holistic approach – what John Virsack of ARM has called the “360 degrees of safety.” Consider workplace programs to promote healthy eating, exercise, work-life balance, and stress reduction. Workers in good shape physically and mentally are less likely to get injured and miss days.
Waste caddies and dumpster movers are a necessity for workers, regardless of physical conditioning. No strong man can safely push and maneuver a loaded dumpster 100% of the time. Frequent exertion, inclines, gravel parking lots, etc. – the job needs automation to be safe.
Consider the many safety hazards of manually moving dumpsters:
• Muscle strains from long-term overexertion.
• Herniated discs, torn muscles from sudden force.
• Crushed fingers and toes, e.g. when maneuvering into a freight elevator.
• Pinned by dumpster when out of control on slope or slippery surface.
• Property damage if dumpster strikes parked cars or buildings.
To prevent worker injuries — not to mention the cost of sick days and workers comp claims — invest in a waste caddy to improve safety for your maintenance staff.