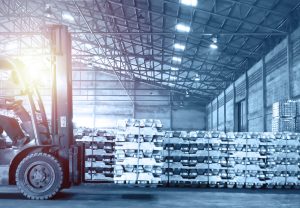
Workplace musculoskeletal disorders (WMSDs) include injuries such as carpal tunnel syndrome, back strains and hernias. Did you know that, in addition to direct treatment costs, WMSDs can cost up to five times as much in indirect costs? Find out how equipment such as our motorized trailer dolly can increase workplace safety and reduce risk of WMSDs.
How Does Ergonomic Motorized Equipment Improve Material Handling Safety?
1. Minimizes strain and fatigue
Excessive stress placed on joints and muscles is one of the leading causes of WMSDs. Employees may lift materials that are too heavy or
perform repetitive motion tasks that create undue strain. Use of motorized equipment takes the physical burden of such activities off the employees, relieving the causes of musculoskeletal stress.
2. Encourages correct posture and position
Have you ever seen workers attempting to extend their reach to retrieve an object on a high rack? Maybe you’ve noticed people bending over to pick up heavy items, rather than bending at the knees and using their legs. When an employee operates our motorized trailer dolly, they can maintain optimum posture as the dolly performs any necessary turns, twists and lifting.
3. Limits time spent on manual tasks
Alarmingly, nearly three-quarters of workers who participate in manual material handling, or MMH, experience back-related pain. These injuries, in turn, account for approximately one-third of compensation costs and lost productivity. Motorized material handling equipment moves items safely and efficiently, without the need for manual labor.
4. Reduces risk of slip-and-drop accidents
Many objects in a warehouse are heavy and bulky or have an irregular shape. This makes it difficult for workers to get a secure grip when handling or transporting these items. As a result, an employee may twist their body or limbs to gain better control, or they may lose their grasp altogether, causing injury to themselves or damage to the item.
Choose the Motorized Trailer Dolly from DJ Products
Are you ready to make safety a priority in your warehouse? Contact us at 800.686.2651, where our knowledgeable Sales Engineers are standing by to help you find the right ergonomic motorized tug, mover or pusher for your application.