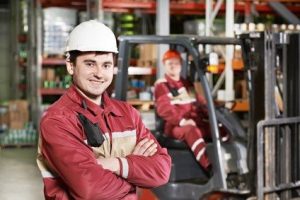
As the warehouse industry gains new facilities in response to the demands of online retailing, companies are taking on inexperienced workers to fill their staffs. Employee onboarding should include training on warehouse equipment as well as appropriate safety tips.
There are basic safety procedures that apply to all warehouses regardless of size and products handled. Protect new and experienced employees by incorporating these safety tips in your company culture.
Top Tips to Prioritize Warehouse Safety
– Safety training is essential for all new hires, but it should also be ongoing to ensure that workers stay current with policies and protocol. Specific areas of focus include warehouse equipment operation, handling of hazardous materials and emergency procedures.
– Is your warehouse organized for optimum safety? Review workflows periodically and make any necessary adjustments to maintain a logical layout.
– Cluttered aisles, dirty warehouse equipment and liquid spills are unsightly and pose serious injury risks. In addition, a sloppy warehouse affects morale and leads to decreased efficiency. Establish cleaning checklists and schedules for all workstations.
– Fire detection and extinguishing systems are set by building codes, but additional measures may be required if hazardous or flammable materials are stored in your warehouse. All fire escape routes should be clearly marked and kept free of obstructions.
– Employees are involved in the day-to-day operations of the warehouse, putting them in a good position to identify hazards that may develop over time. Instruct supervisors to maintain transparent channels of communication with workers so they feel comfortable reporting any problems.
Reduce Workplace Injuries with Warehouse Equipment from DJ Products
We have a battery-powered tug, mover or pusher to accommodate any application in your warehouse. Our friendly sales engineers are available to help you via our convenient online chat feature.